Zastosowanie badań termograficznych wysokiej rozdzielczości w diagnostyce maszyn elektrycznych
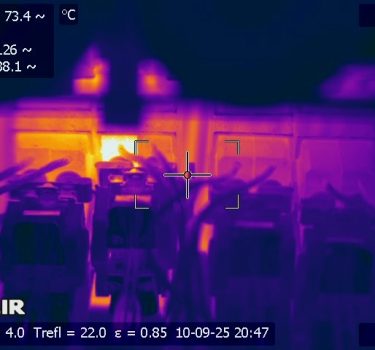
W artykule przedstawiono przykłady wykorzystania technologii badań termograficznych do diagnostyki maszyn elektrycznych stosowanej w praktyce energetyki zawodowej. Szczegółowo omówiono przypadek diagnostyki aparatu szczotkowego turbogeneratora w elektrowni oraz wirnika silnika indukcyjnego dużej mocy.
Poniższy artykuł jest chroniony prawem autorskim. Kopiowanie lub powielanie zawartych w nim treści oraz zdjęć bez zgody autora jest zabronione.
Wstęp
Prawidłowa eksploatacja urządzeń elektroenergetycznych, silników indukcyjnych dużych, średnich mocy, transformatorów energetycznych, rozdzielni energetycznych, wyłączników itp., związana jest zawsze z okresowymi badaniami diagnostycznymi. Pomiary diagnostyczne mają za zadanie, w odpowiednim czasie, ostrzec osoby odpowiedzialne za eksploatację przed mogącą zaistnieć awarią.
Stały postęp w dziedzinie metod diagnozowania i aparatury diagnostycznej dostarcza coraz to więcej informacji o stanie technicznym urządzeń. Uzyskiwana w ten sposób duża ilość informacji, często budzi pewne trudności interpretacyjne, w szczególności w takim przypadku gdy trzeba odpowiedzieć w którym miejscu zlokalizowana jest wcześniej stwierdzona usterka. Pomocą we wskazaniu wcześniej stwierdzonej usterki, może być zastosowanie technologii termograficznej o odpowiedniej rozdzielczości.
W artykule tym, na przykładzie urządzenia szczotkowego turbogeneratora i wirnika silnika indukcyjnego zasygnalizowano możliwość zbierania i porównywania informacji o ich stanie technicznym, korzystając z badań termograficznych.
W ocenie stanu technicznego urządzenia szczotkowego polegającej na analizie temperatury jego pracy, duże znaczenie ma nie tylko jego temperatura bezwzględna, lecz przyrost w stosunku do temperatury sąsiadujących ze sobą szczotek podczas pracy. Temperatura pracy urządzenia szczotkowego przy obciążeniu znamionowym jest z kolei zależna także od temperatury otoczenia i warunków chłodzenia.
Na wykonanie prawidłowych termogramów i analiz badanego urządzenia składa się kilka czynników, między innymi są to:
- Znajomość badanego obiektu.
- Odległości od badanego urządzenia.
- Współczynniki emisyjności.
- Temperatura otoczenia.
- Warunki środowiskowe: nasłonecznienie, zapylenie, opady atmosferyczne, inne źródła promieniowania podczerwonego.
Wymienione warunki nie wyczerpują wszystkich zagadnień związanych z określeniem stanu technicznego techniką termograficzną, pomiar ten na pewno nie może się ograniczyć tylko do mechanicznego wykonania termogramu bez uwzględnienia warunków wymienionych jak wyżej. Dokładna analiza komputerowa zarejestrowanego termogramu może uwidocznić punkty, które na pierwszy rzut oka były niewidoczne, dopiero wspólna analiza wykonanego termogramu i warunków pracy urządzenia może dać obiektywny obraz jego stanu technicznego.
Badanie rozkładu temperatur aparatu szczotkowego turbogeneratora
Bezawaryjna praca turbogeneratora elektrowni zawodowej jest między innymi uzależniona od prawidłowej i bezawaryjnej pracy urządzenia szczotkowego, które jest bezpośrednio odpowiedzialne za wzbudzenie generatora.
Na bezawaryjną pracę urządzenia szczotkowego składają się między innymi takie elementy jak:
– rodzaj zastosowanych szczotek,
– wielkość siły docisku szczotek do pierścienia,
– warunki chłodzenia aparatu szczotkowego.
Często pojawiająca się zbyt wysoka temperatura pracy szczotek, a w następstwie podwyższona temperatura szczotkotrzymaczy i sprężyn dociskowych, może być przyczyną nieprawidłowej pracy pierścieni, a w konsekwencji ich szybszego zużycia.
Podwyższona temperatura pracy szczotek może być spowodowana wieloma przyczynami. Można wydzielić dwa rodzaje przyczyn; przyczyny techniczno-konstrukcyjne oraz przyczyny pośrednie, które są wynikiem tych pierwszych.
Do przyczyn techniczno-konstrukcyjnych należą:
– rodzaj materiału z jakiego zostały wykonane szczotki,
– ustawiona siła docisku szczotek,
– gładkość samych pierścieni,
– jednolitość styku powierzchni szczotki i pierścienia.
Przyczyny pośrednie zależą głównie od symetrii prądowej obciążenia wszystkich szczotek. Może się zdarzyć, że zbyt słaby docisk kilku szczotek do pierścienia wirnika powoduje zmniejszenie przewodności elektrycznej, co może spowodować, że część prądu obciążenia zostaje przejęta przez prawidłowo pracujące szczotki, w skutek czego zaczynają one przewodzić większy niż znamionowy prąd i przegrzewają się. Można zatem wyciągnąć wniosek, że bardzo ważnym elementem poprawnej pracy urządzenia szczotkowego jest równomierne prądowe obciążenie szczotek. Nie bez znaczenia są także warunki środowiskowe chłodzenia szczotek tj.: temperatura, wilgotność powietrza chłodzącego.
Wszystkie te anomalie temperaturowe szczotek wymagają dokładnej analizy ich pracy w celu ustalenia przyczyn i środków zaradczych. Dokładną analizę pracy można wykonać przy zastosowaniu kamery termograficznej wysokiej rozdzielczości, w tym wypadku rozdzielczości obrazowej 640 x 480 linii i rozdzielczości temperaturowej poniżej 0,1oC. Rysunek 1 przedstawia termogram pracy szczotek nałożony na zdjęcie oraz sam termogram. Poniżej zamieszczono wykres rozkładu temperatury wzdłuż zaznaczonego odcinka.
Rys.1. Termogram nałożony na zdjęcie części aparatu szczotkowego, ten sam termogram w barwie gorącego żelaza oraz wykres rozkładu temperatury na badanych szczotkach
Badania termograficzne klatki wirnika
Kolejnym przykładem jest diagnostyka klatki wirnika silnika indukcyjnego.
W ostatnich latach zmniejszyła się znacznie ilość uszkodzeń silników elektrycznych WN eksploatowanych w elektrowniach. Jak podaje [1] współczynnik awaryjności podający stosunek ilości silników uszkodzonych w ciągu roku do ilości silników zainstalowanych zmniejszył się w ostatnich dziesięciu latach co najmniej kilkanaście razy. Wiąże się to ewidentnie z coraz większym stosowaniem profilaktycznych badań diagnostycznych, doskonaleniem aparatury diagnostycznej, a także większą kulturą eksploatacji napędów. Spotykane uszkodzenia silników indukcyjnych WN stosowanych w elektrowniach węglowych sprowadzają się głównie do uszkodzeń obwodów elektrycznych, czyli klatek i uzwojeń stojanów oraz łożysk. Przyczynami uszkodzeń mogą być zjawiska zewnętrzne takie jak np. przepięcia sieciowe i łączeniowe, odkształcenia napięcia zasilania od kształtu sinusoidalnego, zagrożenia środowiskowe takie jak zawilgocenie, zapylenie itp. Przyczynami mogą być także zjawiska związane z normalną eksploatacją silników a więc rozruchy, przede wszystkim rozruchy długie lub często powtarzające się po sobie. Przyczyną uszkodzeń mogą być też przeciążenia silników.
W wyniku uszkodzenia klatki silnika indukcyjnego powstaje nie symetria obwodu elektrycznego wirnika. Jest ona przyczyną powstania składowej przeciwnej kolejności pola magnetycznego, a jej skutkiem jest pojawienie się w prądzie zasilania składowych o tzw. częstotliwościach poślizgowych (1-2s)f oraz (1+2s)f, gdzie f oznacza częstotliwość napięcia zasilania, a s poślizg wirnika. Pomiar tych diagnostycznych składowych w prądzie zasilania jest możliwy w trakcie normalnej eksploatacji silników, ale wymaga to obciążenia silnika co najmniej połową znamionowego momentu obciążenia. Podczas rozruchu występuje również składowa o zmniejszającej się amplitudzie i częstotliwości (1-2s)f, która przy połowie prędkości synchronicznej spada do zera. Obie te metody dobrze się uzupełniają, a ich porównanie przeprowadzono w [2]. Metody te pozwalają na prowadzenie okresowych badań diagnostycznych klatek, archiwizację danych, obserwację trendów i w ten sposób przez analizę wyników w czasie, pewną ocenę aktualnego stanu klatek. W przypadku silników dwuklatkowych obie te metody nie są równoważne, pomiary diagnostyczne prądu rozruchowego dają informację przede wszystkim o stanie klatki górnej (rozruchowej), a pomiary prądu zasilania obciążonego silnika o stanie klatki dolnej (pracy). Pomimo tego, że metody te są wystarczające aby ocenić stan klatki, może zachodzić potrzeba lokalizacji uszkodzenia klatki. Do tego celu dobrze nadaje się metoda termograficzna. Metoda ta pozwala dodatkowo na oceną stanu obwodu magnetycznego (żelaza wirnika).
Metoda termograficzna zastosowana do analizy stanu obwodów elektrycznych wirnika zrealizowana została w oparciu o rejestrację rozkładu temperatur (termogramów) kamerą termowizyjną o rozdzielczości poniżej 0,1°C. Istotnym elementem metody jest wymuszenie prądu w obwodach elektrycznych klatki wirnika tak, żeby możliwa była obserwacja wizualna wszystkich połączeń prętów klatki i blach żelaza czynnego. W tym celu badany wirnik silnika indukcyjnego został włożony do stojana silnika indukcyjnego o większej średnicy, wirnik został ustawiony symetrycznie w stosunku do osi stojana. Sposób włożenia wirnika przedstawiono na rysunku 2.
Rys.2. Nagrzewanie wirnika silnika indukcyjnego
Kolejnym krokiem było wymuszenie przepływu prądu w obwodach klatki wirnika. W tym celu stojan silnika opisanego wyżej został zasilony 3-fazowo ze źródła o mocy 1,2 MW o regulowanym napięciu i częstotliwości. Wytworzony strumień magnetyczny wymusza prąd w obwodach klatki wirnika. Regulację wartości napięcia zasilania dostosowano tak, żeby przyrost temperatury był około 2 °C/min. Mimo posadowienia wirnika jak na rysunku 2, w czasie nagrzewania nie stwierdzono drgań wirnika.
Sprawdzenie obwodów elektrycznych klatki wirnika polegało na sprawdzeniu połączeń prętów klatki z pierścieniem zwierającym, oraz sprawdzeniu czy nie ma lokalnych znacznych przyrostów temperatury na powierzchni żelaza czynnego wirnika. Wcześniej badany wirnik został poddany oględzinom zewnętrznym, podczas których stwierdzono pęknięcia mocowania prętów klatki, zgięcie prętów przy pierścieniu zwierającym i rozwarstwienie powierzchni żelaza czynnego Defekty te przedstawiają rysunki 3, 5 i 6
Rys.3. Zdjęcie z nałożonym termogramem pękniętego połączenia pręta klatki z pierścieniem
Rys.4. Wykresy rozkładu temperatury połączenia pręta wirnika z pierścieniem z rys. 3
Rys.5. Pęknięte połączenie pręta wirnika z pierścieniem
Po podłączeniu zasilania nagrzewanie wirnika było monitorowane kamerą termowizyjną. Na wszystkich nagrzewających się powierzchniach połączeń prętów klatki z pierścieniem zostały wykonane termogramy. Wszystkie zarejestrowane termogramy zostały poddane wnikliwej analizie komputerowej. Analiza ta polegała m.in. na dobraniu odpowiedniej skali barw, którym były przyporządkowane określone wielkości temperatur oraz wykonaniu histogramów rozkładu temperatur na analizowanych powierzchniach.
W analizie tej [3] istotą zagadnienia było wykrywanie znaczących względnych różnic temperatur. Wielkość maksymalnej temperatury ulegała zmianie wraz z upływem czasu nagrzewania się wirnika, nie miało to jednak większego znaczenia, ograniczeniem była tylko maksymalna wartość temperatury, do której mógł się nagrzać wirnik, założono, że temperatura ta nie może przekroczyć 120°C.
Po dokonaniu analizy wykryto w ten sposób dwa razy tyle defektów niż przy oględzinach zewnętrznych. Przykłady analizy termogramów połączeń prętów przedstawiają rysunki 3 i 4. Zamieszczono tutaj wykresy rozkładu temperatur dwóch połączeń pręta z pierścieniem, kolor czerwony obrazuje rozkład temperatury na uszkodzonym połączeniu zęba pierścienia z prętem klatki (numer 46 na rysunku 3). Wykorzystując analizę termogramu można kontrolować stan techniczny żelaza wirnika. Wykres rozkładu temperatur na rysunku 8 zobrazowuje rozkład temperatury wzdłuż zaznaczonego odcinka L1 na rysunku 7. Rozkład temperatury jest typowy dla sprawnego wirnika, w przypadku pojawienia się piku na wykresie oznaczałoby, że odpowiednio w danym miejscu jest zwarcie w blachach żelaza.
Rys.6. Uszkodzona powierzchnia wirnika
Rys.7. Termogram żelaza czynnego badanego wirnika nałożony na fotografię wirnika
Rys.8. Wykres rozkładu temperatury na powierzchni wirnika
Wnioski
Zastosowanie nowoczesnego narzędzia diagnostycznego jakim jest kamera termograficzna wysokiej rozdzielczości do analizy wszelkiego rodzaju połączeń obwodów elektrycznych, wraz ze zrozumieniem zjawisk występujących w analizowanym urządzeniu, jest bardzo skutecznym narzędziem oceny jego stanu technicznego.
Analizowany termogram badanego urządzenia potwierdza często informacje uzyskane innymi metodami o defektach technicznych urządzenia z tym, że dodatkowo umożliwia ich dokładną lokalizację.
LITERATURA
[1] BERNATT M. O awaryjności silników klatkowych wysokiego napięcia. Zeszyty Problemowe KOMEL nr 68/2004, str.37-40. [2] RAMS W, RUSEK J. Praktyczna diagnostyka maszyn indukcyjnych klatkowych. Zeszyty Problemowe KOMEL nr 68/2004, str.1-5. [3] Ławrowski Z.: Diagnostyka silników klatkowych wysokiego napięcia w energetyce. Praca doktorska, Politechnika Śląska Gliwice, 1999r. [4] Hickiewicz J., Ławrowski Z.: Diagnostyka maszyn elektrycznych w elektrowniach – przykłady praktyczne. Zeszyty Problemowe KOMEL nr 71/2005, str.71-79.